В современном мире, где безопасность и надежность инфраструктуры становятся ключевыми факторами, предприятия, занимающиеся строительством трубопроводов, стремятся обеспечить высокое качество своих работ. Одним из основных этапов в этом процессе является дефектоскопия — система методов и технологий, позволяющих выявлять дефекты в сварных швах и трубах без их разрушения. Давайте разберёмся, как именно осуществляется эта проверка и какие её основные этапы.
Зачем нужна дефектоскопия трубопроводов?
Дефектоскопия трубопроводов — это комплекс методов и технологий, позволяющий выявлять дефекты в материалах, конструкциях и сварных швах трубопроводов без их разрушения. То есть, дефектоскопия производится прямо на строительной площадке. Стыки труб не разрушаются, что снижает себестоимость монтажных работ. Это важный процесс, который помогает удостовериться в надежности трубопроводов.
Почему дефектоскопия трубопроводов важна?
1. Обеспечение безопасности
Более 80% аварий, связанных с трубопроводами, происходят из-за повреждений, возникших в результате высоких нагрузок или ненадежных сварных соединений. Если не провести своевременную проверку, возможны утечки или даже взрывы, что представляет серьезную угрозу для здоровья людей и экологии. Дефектоскопия позволяет выявлять такие проблемы до того, как они станут катастрофой.
2. Экономическая целесообразность
Ремонт поврежденных трубопроводов — это не только затраты на работы, но и потеря ресурсов, времени и снижение производительности. Предотвращение аварий и неисправностей через регулярный контроль состояния трубопроводов может значительно снизить финансовые риски и избежать дорогостоящих остановок в работе.
3. Соответствие стандартам
Каждая страна имеет свои стандарты и требования к строительству и эксплуатации трубопроводов. Дефектоскопия является обязательным этапом для обеспечения соответствия этим нормам. Контроль качества необходим для соблюдения законодательства и поддержания репутации компании.
4. Долговечность трубопроводов
Проверка сопоставления сварных швов и труб позволяет определить, подходят ли они для дальнейшей эксплуатации. Это особенно важно на этапе пуска и наладки системы, когда выявление проблем может существенно повлиять на срок службы трубопровода. Проведение дефектоскопии обеспечивает возможность максимально долгой и безопасной эксплуатации.
Дефекты сварных швов и соединений трубопроводов
Сварные швы и соединения трубопроводов играют ключевую роль в надежности и безопасности любых трубопроводных систем. Они являются теми местами, где различные стальные компоненты соединяются в единое целое. В то время как качественно выполненные сварные швы способны прочитать высокие нагрузки и выдерживать длительное воздействие агрессивных сред, дефекты, возникающие во время сварки, могут привести к серьезным авариям, утечкам и даже затратам на восстановление и замену. В этой статье мы подробно рассмотрим основные виды дефектов сварных швов и соединений трубопроводов, причины их возникновения, а также методы контроля и предотвращения.
Существуют различные типы дефектов, которые могут возникнуть в процессе сварки трубопроводов. Их можно классифицировать на несколько основных категорий.
1. Непровары
Непровары – это дефект, возникающий, когда сварочный материал не проникает полностью в стыковую зону соединяемых деталей. Это может привести к снижению прочности соединения и увеличению вероятности его разрушения при эксплуатации.
Непровары могут быть следствием недостаточной температуры или скорости сварки, неправильного выбора электрода или недостаточной подготовки к стыковке.
2. Поры
Поры — это шарообразного вида дефекты (форма может быть и другой, но всегда полой), образующиеся за счет газов, которые выделяются в процессе сварки металла. Они могут находиться как на поверхности, так и внутри шва, и, в зависимости от их размеров и расположения, могут значительно ослабить прочность соединения. Основными причинами образования пор являются низкое качество сварочных материалов, неправильная подготовка поверхности и наличие загрязнений. Поры могут сокращать прочность соединения и вызывать коррозию из-за накопления жидкости в них, что может стать предпосылкой к повреждениям и утечкам.
3. Трещины
Трещины могут возникать как в процессе сварки, так и после ее завершения. Они могут быть вызваны неправильными режимами сварки, охлаждением или напряжениями, возникающими внутри материала. Причиной трещин могут быть также остаточные напряжения, возникающие при охлаждении. Трещины — это наиболее опасный тип дефектов, так как они могут быстро прогрессировать и привести к катастрофическому разрушению соединения.
4. Подрезы. Образуются на границе торцов труб и сварного шва. За счет этого уменьшается площадь соприкосновения двух металлов. На таких участках увеличивается внутреннее напряжение, особенно, когда увеличивается нагрузка на трубопровод.
5. Наплывы. Это слой металла, который накладывается на поверхность шва. Получается так, что верхний и нижний слои практически ничем не связаны. Сечение соединения не такое, как требуется по ГОСТу.
6. Коррозия
Хотя коррозия не относится непосредственно к сварке, она может развиваться в тех местах, где швы повреждены. Плохая защита от коррозии или некачественные сварные соединения могут привести к значительному сокращению срока службы трубопроводов.
Методы неразрушающего контроля сварных швов трубопроводов
Трубопроводы — это важные компоненты в различных отраслях, включая нефтегазовую, химическую и водоснабжающую. Сварные швы играют ключевую роль в обеспечении их безопасности и надежности. Для оценки качества этих швов применяется неразрушающий контроль (НК) — метод, который позволяет выявить дефекты без повреждения материала.
Требования к качеству сварных соединений трубопроводов регламентируются различными стандартами и нормативами.
Неразрушающий контроль сварных швов трубопроводов позволяет:
- Определить возможные дефекты и повреждения в трубопроводах без их разрушения или прекращения работы
- Предотвращать аварии. Обнаружение скрытых дефектов до их превращения в серьезные проблемы.
- Снижать затраты. Более эффективное использование ресурсов способствует снижению эксплуатационных расходов и уменьшению потерь.
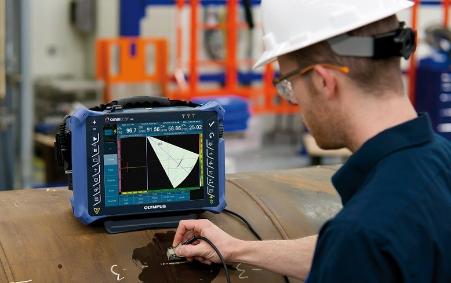
Визуальный контроль сварных швов трубопроводов
Визуальный контроль сварных швов трубопроводов — это один из наиболее распространенных и доступных методов неразрушающего контроля, который играет ключевую роль в оценке качества трубопроводов. Если говорить о надежности трубопроводных систем, каждый шов должен отвечать строгим стандартам, так как именно в этих местах чаще всего происходят дефекты, способные привести к серьезным авариям.
Визуальный контроль — это первый и самый простой шаг в процессе инспекции. Он не требует сложного оборудования и может быть проведен с помощью простых инструментов, таких как линейки, уровни и лупы. Основная задача визуального контроля — обнаружить видимые дефекты на сварных швах, такие как:
- Отсутствие соединения в некоторых участках
- Неправильная форма и размеры шва
- Трещины, каверны и поры
- Неровности и отслоения
Методы проведения визуального контроля
- Обычный визуальный осмотр. Исполнитель изучает швы с использованием обычного освещения, проверяя наличие видимых дефектов.
- Использование вспомогательных инструментов. Лупы и специализированные отражатели могут помочь в обнаружении мелких недостатков, которые могли бы ускользнуть от зрения при обычном осмотре.
- Актуальные нормы и стандарты. Важно следовать установленным стандартам, таким как ГОСТ и ISO, которые определяют, что именно проверять и какие отклонения считать допустимыми.
Визуальный контроль является краеугольным камнем в процессе обеспечения качества на всех этапах — от проектирования до эксплуатации. Он позволяет:
- Раннее выявление дефектов, что может значительно сократить будущие затраты на ремонт и эксплуатацию.
- Повышение доверия к качеству работ за счет строгого соблюдения требований.
- Своевременное вмешательство, если качество сварных швов не соответствует стандартам, что может предотвратить серьезные аварии.
Важно понимать, что визуальный контроль не является единственным методом. Однако он служит важной отправной точкой для более тщательных исследований с использованием других методов неразрушающего контроля, таких как ультразвуковая или радиографическая инспекция. В конечном итоге, соблюдение высокого качества сварных швов — это залог безопасности и надежности трубопроводных систем, что делает визуальный контроль неотъемлемой частью процесса контроля качества.
Ультразвуковой контроль сварных швов и соединений трубопроводов
Ультразвуковой контроль — это один из самых надежных и точных методов неразрушающего контроля, который широко используется в промышленности для оценки качества сварных швов и соединений трубопроводов. Этот метод основывается на использовании высокочастотных звуковых волн, которые проходят через материал и отражаются от его внутренних дефектов или границ раздела.
Ультразвуковой контроль представляет собой процесс, при котором ультразвуковые волны генерируются пьезоэлектрическими преобразователями. Эти волны проникают в материал трубы или сварного соединения, и, столкнувшись с различными структурами (включая дефекты, такие как трещины, поры и включения), они отражаются обратно к преобразователю. Анализ полученных сигналов позволяет специалистам определить наличие и характер дефектов.
Преимущества ультразвукового контроля сварных швов и соединений трубопроводов
- Высокая чувствительность, т.е. способность метода обнаруживать даже малые дефекты или изменения в материале, что позволяет выявлять микротрещины, поры и другие недостатки, которые могут негативно сказаться на прочности и надежности сварных швов и соединений трубопроводов. Такая характеристика делает ультразвуковой контроль одним из самых эффективных методов неразрушающего контроля в промышленности.
- Глубина проникновения. Ультразвук проникает на значительные глубины, что позволяет контролировать толстостенные конструкции, такие как трубопроводы.
- Измерение толщины. Метод используется не только для обнаружения дефектов, но и для контроля толщины стенок трубы, что критично для выявления коррозии.
- Безопасность. Ультразвуковой контроль является неразрушающим, что позволяет сохранять функциональность трубопроводов без необходимости их демонтажа или замены.
Ультразвуковой контроль сварных швов и соединений трубопроводов является неотъемлемой частью процесса обеспечения качества трубопроводов. Он не только позволяет выявлять и классифицировать дефекты, но и способствует снижению рисков, связанных с эксплуатацией трубопроводов. Используя данный метод, предприятия могут гарантировать долгосрочную надежность и безопасность своих систем, что, в конечном счете, приводит к экономии ресурсов и увеличению доверия со стороны клиентов.
Радиографическая дефектоскопия сварных швов и соединений трубопроводов
Радиографическая дефектоскопия (РК) является одним из самых популярных и эффективных методов неразрушающего контроля, используемым для оценки качества сварных швов и соединений трубопроводов. Этот метод опирается на применение ионизирующего излучения для визуализации внутренних структур материалов, что позволяет выявлять дефекты, такие как трещины, поры и несплавления.
Для этого используются рентгеновские или гамма-излучающие источники, которые направляются на проверяемую область. Излучение проходит через материал и регистрируется на фотопленке или цифровом детекторе. Различия в плотности и толщине материалов приводят к различным уровням поглощения излучения, что позволяет выявлять внутренние дефекты.
Преимущества метода:
- Высокая разрешающая способность. Радиографические снимки обладают высокой детализацией, что позволяет обнаруживать даже мелкие и тонкие дефекты.
- Полная оценка структуры. Метод обеспечивает визуализацию всего поперечного сечения соединения, что даёт полное представление о состоянии сварного шва.
- Объективность. Результаты радиографической дефектоскопии можно объективно оценивать и документировать, что важно для соблюдения стандартов и норм.
- Непосредственная оценка. Компании зачастую требуют предоставление визуальных отчетов, и радиографические снимки могут служить наглядными доказательствами качества сварных соединений.
Несмотря на множество преимуществ, радиографическая дефектоскопия также имеет свои ограничения. К примеру, она требует значительных мер безопасности, поскольку работа с ионизирующим излучением подразумевает риски для здоровья. Проводить такую дефектоскопию необходимо в специально оборудованных помещениях, где соблюдены все нормы безопасности.
Схема проверки выглядит так: на место сварного шва устанавливают аппарат, который излучает рентгеновские лучи, проникающие в металл. Если присутствуют дефекты, излучение выходит наружу большей интенсивности. Если же структура плотная, изъянов в ней нет, — луч проходит меньшей интенсивности. Аппарат фиксирует проникновение лучей, делает снимок, на котором можно увидеть расположение и размер дефектов.
РК считается одним из самых точных методов проверки качества соединений. Его применяют при проверке труб, металлоконструкций, разных изделий. Поэтому важно использовать данный метод в сочетании с другими способами контроля, такими как ультразвуковая или магнитопорошковая дефектоскопия, чтобы получить более полное представление о качестве трубопровода.
Радиографическая дефектоскопия является незаменимым инструментом в арсенале методов неразрушающего контроля. Она обеспечивает высокую степень достоверности и точности при выявлении дефектов в сварных швах и соединениях трубопроводов. Правильное применение этого метода, включая соблюдение норм безопасности и комбинирование с другими методами контроля, поможет предприятиям обеспечить надежность и долговечность своих трубопроводных систем, что, в конечном итоге, приводит к снижению затрат на обслуживание и увеличению безопасности эксплуатации.
Магнитная дефектоскопия сварных швов и соединений трубопроводов
В современном строительстве трубопроводов безопасность и надежность являются ключевыми аспектами. Одним из наиболее эффективных методов неразрушающего контроля, используемым для проверки качества сварных швов и соединений, является магнитная дефектоскопия. Этот метод особенно актуален для трубопроводов, принимая во внимание их важность в транспортировке различных жидкостей и газов.
Магнитная дефектоскопия основана на использовании магнитного поля для выявления дефектов в материалах. При проведении контроля электрический ток пропускается через проводник, создавая магнитное поле. Когда магнитное поле воздействует на сварной шов, оно изменяется в области дефектов, таких как трещины, поры или некорректные сплавы. Эти изменения фиксируются с помощью магнитной порошковой или магнитной флуоресцентной технологии.
Первый этап включает в себя предварительное разрушение охватываемой зоны, что позволяет порошку или флуоресцентной жидкости «попасть» в дефекты. На следующем этапе проводятся визуальные исследования, которые позволяют оценить состояние сварного шва и выявить наличие дефектов.
Преимущества магнитной дефектоскопии:
- Высокая чувствительность к поверхностным и подповерхностным дефектам. Магнитная дефектоскопия хорошо подходит для выявления трещин и пор, которые могут угрожать целостности трубопровода.
- Быстрота и простота метода. Процедура проверки может быть выполнена за относительно короткое время, что важно для поддержания графика строительства.
- Отсутствие необходимости в предварительных подготовках. В отличие от некоторых других методов контроля, магнитная дефектоскопия может быть проведена на необработанных поверхностях и не требует сложной подготовки материалов.
- Экономичность. Использование магнитных порошков и растворителей делает этот метод более доступным в сравнении с другими видами неразрушающего контроля.
Несмотря на явные преимущества, магнитная дефектоскопия имеет свои ограничения. Метод эффективен только для черных металлов и сплавов с высокой магнитной проницаемостью. Также важно учитывать, что данный метод не позволяет выявить дефекты, находящиеся на глубине, поскольку магнитные поля не проникают глубоко в материал.
Магнитная дефектоскопия является мощным инструментом для контроля сварных швов и соединений трубопроводов. Благодаря своей высокой чувствительности и экономичности этот метод находит широкое применение в различных отраслях, включая энергетику, нефтегазовую промышленность и машиностроение. Инвестиции в качественный контроль сварных соединений обеспечивают надежность трубопроводов и, как следствие, безопасность конечного продукта, что и делает этот метод столь востребованным.
Капиллярный метод в неразрушающем контроле сварных швов и соединений трубопроводов
В сфере строительства трубопроводов надежность и безопасность систем транспортировки различных веществ стоят в центре внимания. Одним из наиболее ценимых методов неразрушающего контроля, позволяющим тщательно проверять качество сварных швов и соединений, является капиллярный метод. Этот метод зарекомендовал себя как эффективный способ выявления и анализа поверхностных дефектов, что особенно критично для долговечности и безопасности трубопроводных систем.
В основе капиллярного метода неразрушающего контроля лежит использование контрастного вещества (пенетранта), которое, проникая в различные дефекты, образует под воздействием капиллярного давления визуализируемые индикаторные рисунки. На основании полученных рисунков можно выявить не только количественный, но и качественный состав повреждений.
Преимущества капиллярного метода:
- Высокая чувствительность. Метод способен обнаруживать самые мелкие дефекты, что особенно важно при контроле критически важных соединений трубопроводов.
- Универсальность. Капиллярный метод может применяться к различным материалам, включая сталь, алюминий и даже композитные материалы.
- Минимальная подготовка. Процесс контроля не требует значительных временных затрат на подготовку, что позволяет ускорить процесс проверки.
- Низкие затраты. Используемые реагенты и оборудование относительно недороги по сравнению с другими методами неразрушающего контроля, такими как ультразвуковая дефектоскопия.
- Частые применения и рекомендации
Капиллярный метод широко используется в различных отраслях, где качество сварных соединений имеет критическое значение, включая нефтяную, газовую и химическую промышленности. Для успешного применения метода необходимо следовать рекомендации производителя проникающих и проявляющих средств, а также учитывать особенности исследуемого материала.
Капиллярный метод неразрушающего контроля представляет собой мощный инструмент для оценки качества сварных швов и соединений трубопроводов. Его преимущества — высокая чувствительность, универсальность, простота и экономичность — делают его незаменимым для предприятий, стремящихся обеспечить безопасность и надежность своих систем. Поддерживая высокие стандарты контроля качества, вы можете минимизировать риск аварий и продлить срок службы трубопроводов, способствуя тем самым устойчивому развитию отрасли.

Почему стоит работать с “ТПЭ-АТОМ”?
Дефекты стыков трубопроводов — это серьезная проблема, которая может повлечь за собой высокие риски для безопасности и устойчивости всей системы. Знание основных видов дефектов, причин их возникновения и методов диагностики позволяет избежать серьезных последствий. Эффективный контроль качества сварных соединений с использованием неразрушающих методов и адекватные меры по устранению дефектов — ключ к безопасной и надежной эксплуатации трубопроводов. Оптимизация процессов сварки и улучшение квалификации персонала помогут значительно повысить качество конечного продукта, что является основной задачей для предприятий, работающих в данной области.
Если вы ищете квалифицированных специалистов в области неразрушающего контроля, наша лаборатория предлагает профессиональные услуги визуально-измерительного контроля трубопроводов. Мы обеспечим высокий уровень проверки, проведем анализ состояния ваших трубопроводных систем и предоставим подробный отчет с рекомендациями. Не рискуйте безопасностью вашего бизнеса – доверьте контроль качества нам!