Проблема надежности трубопроводных систем остается во главе угла промышленных и энергетических предприятий, так как от качества их строительства зачастую зависит безопасность человека и окружающей среды. Выявление дефектов в сварных швах и материалах трубопровода — непреложная задача, которую решает неразрушающий контроль (НК). Эта технология позволяет диагностировать состояние трубопроводов, не нарушая их целостности, и выявлять возможные дефекты на ранних стадиях
Зачем нужен неразрушающий контроль трубопроводов?
Неразрушающий контроль трубопроводов представляет собой систематический процесс оценки качества и характеристик материалов и конструкций без их разрушения. Для трубопроводов он необходим по ряду причин:
- Безопасность. Любые утечки или повреждения трубопровода могут привести к серьезным последствиям, включая экологические катастрофы и угрозу для жизни людей.
- Экономия. Заблаговременное выявление дефектов позволяет снизить затраты на ремонт и техническое обслуживание.
- Соответствие стандартам. Для обеспечения должного качества и безопасности трубопроводов необходимо соответствовать ряду стандартов и нормативов, что также требует проведения НК.
- Долговечность. Понимание состояния трубопроводов и своевременное устранение дефектов способствуют увеличению их срока службы.
Разновидности дефектов трубопроводов: как их распознать и предотвратить
Трубопроводы — это артерии промышленности, обеспечивающие транспортировку жидкостей и газов от точки А до точки Б. Однако, как и любой другой инженерный элемент, они подвержены различным дефектам, которые могут привести к серьезным последствиям.
Дефекты трубопроводов можно классифицировать по разным критериям. В зависимости от причин возникновения их можно разделить на производственные, эксплуатационные и конструктивные.
1. Производственные дефекты
Эти дефекты возникают на этапе производства труб и их сварки. К ним относятся:
- Некачественная сварка. Неправильные параметры сварки могут привести к образованию пор, трещин и непроваров. Некачественная сварка — это одна из самых распространенных причин дефектов сварных швов и соединений, которые негативно сказываются на прочности и безопасности эксплуатации готовых металлоизделий
- Дефекты поверхности. Включают в себя царапины, вмятины и коррозию, которые могут возникнуть в процессе транспортировки или обработки труб. Даже мелкие дефекты могут стать началом большого разрушения.
- Неправильная обработка материалов. Например, использование стали низкого качества или недостаточная закалка.
2. Эксплуатационные дефекты
Эксплуатационные дефекты возникают в результате использования трубопроводов в реальных условиях. К ним относятся:
- Коррозия. Возможна как внутреннее (разрушение стенок трубы из-за жидкости), так и внешнее (воздействие окружающей среды). Коррозия — один из самых опасных видов дефектов, так как она может развиваться незаметно и привести к серьезным авариям.
- Усталостное разрушение. Причиной его может стать постоянное воздействие механических нагрузок или температурных колебаний. Этот дефект часто возникает в местах сварки или изгибов труб.
- Смещения и деформации. Возникают в результате изменения температуры, давления или физических воздействий (например, землетрясений). Они могут приводить к образованию трещин и утечкам.
3. Конструктивные дефекты
Это дефекты, выражающиеся в несоответствий требованиям технологического задания или установленных правил разработки (модернизации) продукции. Конструктивные дефекты представляют собой отклонения от требований технологического задания или установленных правил проектирования. Они могут проявляться в различных формах и приводить к серьезным проблемам в эксплуатации. К основным видам таких дефектов относятся:
- Ошибка выбора материала: Неправильный выбор материала может привести к несовместимости с рабочей средой, вызывая коррозию или деформацию.
- Неверные размеры деталей: Неправильное заданные размеры могут привести к проблемам сборки или неравномерному распределению напряжений.
- Ошибки в термообработке: Неправильные режимы термообработки могут ухудшить механические свойства материала, такие как хрупкость или твёрдость.
- Недочёты в проектировании: Недостаточное внимание к деталям конструкции, таким как недостаточная жёсткость или плохая виброустойчивость.
Основные причины возникновения конструктивных дефектов в трубопроводах можно разделить на несколько категорий:
- Человеческий фактор. Ошибки, допущенные на этапе проектирования из-за недостаточной квалификации специалистов или небрежности.
- Недостаточное исследование условий эксплуатации. Проектировщики могут не учитывать полностью условия, в которых будет эксплуатироваться трубопровод, что приводит к неправильным решениям.
- Отсутствие или неэффективность стандартов и методик. Несовершенные или устаревшие нормативы могут привести к тому, что конструкция теряет свою актуальность и не соответствует современным требованиям.
- Несовершенные программные продукты или ошибки в проведении моделирования могут привести к неправильным конструкционным решениям.
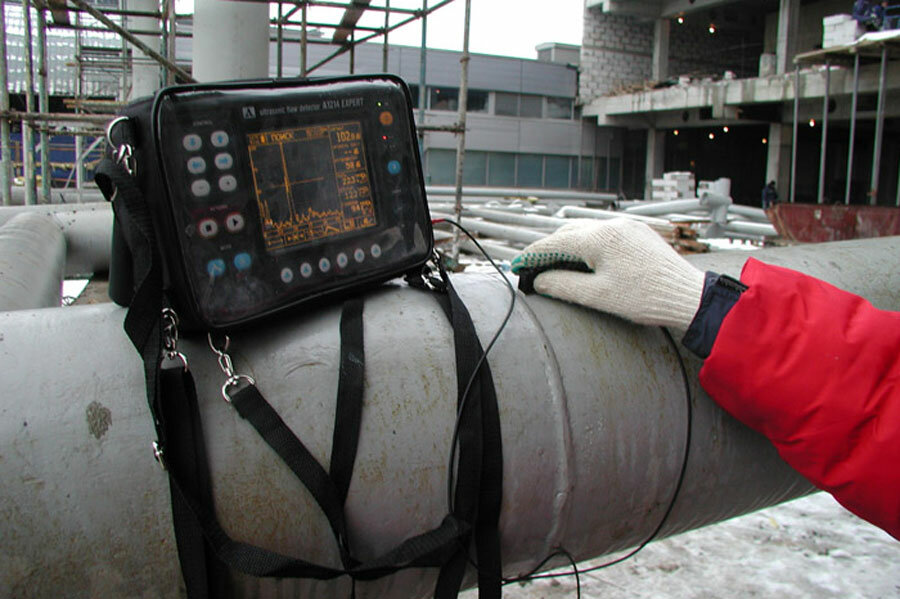
Визуальный контроль трубопроводов
Неразрушающий контроль трубопроводов — важный аспект обеспечения их качества и безопасности. Одним из наиболее доступных и простых методов, который используется на всех этапах — от проектирования до эксплуатации, является визуальный контроль. Несмотря на свою простоту, этот метод требует квалифицированного подхода и внимательного анализа. В данной статье мы рассмотрим, как правильно проводить визуальный контроль трубопроводов, его преимущества, ограничения и практические рекомендации.
Визуальный контроль трубопроводов представляет собой метод, при котором инспектор осматривает трубопроводы на предмет видимых дефектов. Это может быть проверка не только поверхностей труб, но и их соединений, изоляции, опорных систем, а также состояния окружающей среды. Этот метод имеет ряд преимуществ:
- Доступность и простота. Визуальный контроль не требует сложного оборудования, что делает его доступным для большинства предприятий. Контролер может быстро проводить осмотр и документировать результаты.
- Скорость. Визуальный контроль может быть выполнен достаточно быстро и не занимает много времени, в отличие от других методов неразрушающего контроля.
- Первоначальная диагностика. Он позволяет получить предварительное представление о состоянии трубопроводов, выявить очевидные дефекты, такие как коррозия, трещины, износ или повреждения.
- Сокращение затрат. Меньше времени на проверку означает меньшие затраты на техническое обслуживание и ремонты.
Визуальный контроль трубопроводов следует проводить по четкому алгоритму:
- Общее обследование. Осмотрите целостность трубопровода на связи с его окружением. Обратите внимание на возможные утечки, следы коррозии и источники внешнего воздействия.
- Детальный осмотр. Проверьте сварные швы, соединения, опоры и изоляцию. Используйте дополнительные инструменты для выявления скрытых дефектов, если это необходимо.Документация результатов. Все обнаруженные дефекты должны быть задокументированы с подробными описаниями, фотографиями и рекомендациями по дальнейшим действиям.
- Оценка состояния
После проведения осмотра важно правильно оценить найденные дефекты. Классифицируйте их по уровням критичности и определите, требуют ли они немедленных действий, или могут быть запланированы на более поздний срок.
Несмотря на свои плюсы, визуальный контроль трубопроводов имеет и свои ограничения:
- Значительные ограничения по размеру изъянов: 0,1-0,2 мм;
- Невысокая точность измерений;
- Возможность обнаружения только видимых с внешней стороны дефектов и подозрения на возможные повреждения внутри;
- Субъективность в оценке многих видов дефектов.
Однако очевидные преимущества настолько велики, что этот метод используется практически везде с дополнением другими способами контроля, позволяющими исключить имеющиеся недостатки.
Визуальный контроль трубопроводов является важным инструментом для обеспечения их надежности и безопасности. Компетентное выполнение данного вида контроля позволяет своевременно выявлять и устранять дефекты, предотвращая возможные аварии и затраты на восстановление. Тем не менее, важно учитывать его ограничения и использовать его в сочетании с другими методами неразрушающего контроля для достижения наиболее полных и надежных результатов. Осуществление качественного визуального контроля трубопроводов — это не только задача контролера, но и залог безопасности и долговечности всей трубопроводной системы.
Капиллярный метод контроля трубопроводов
Капиллярные методы основаны на капиллярном проникновении индикаторных жидкостей в полости поверхностных и сквозных несплошностей материала объектов контроля и регистрации образующихся индикаторных следов визуальным способом.
Капиллярный метод, также известный как капиллярная дефектоскопия, основан на применении капиллярных жидкостей. В его основе лежит использование красителей или флуоресцентных жидкостей, которые проникают в мелкие трещины, зазоры и поры. После завершения процедуры контроля применяются различные способы обнаружения и визуализации этих проникающих жидкостей, что позволяет четко увидеть области с дефектами.
Процесс контроля трубопроводов включает несколько этапов:
- Подготовка поверхности. Перед началом контроля необходимо очистить поверхность трубопровода от загрязнений, масел, ржавчины и краски. Это обусловлено тем, что любые посторонние вещества могут затруднить проникновение капиллярной жидкости.
- Нанесение капиллярной жидкости. Жидкость равномерно наносится на поверхность трубопровода. Важно выбрать подходящий состав, учитывающий материал трубы и специфику проверки.
- Время проникновения. Капиллярная жидкость должна иметь достаточное время для проникновения в дефекты, после чего излишки жидкости удаляются с поверхности.
- Обнаружение дефектов. Для визуализации использует специальное освещение (например, ультрафиолетовые лампы) и проявляющие растворы, которые активируют трассирующие красители. Инспектор оценивает полученные результаты, фиксируя дефекты.
Капиллярный метод контроля трубопроводов имеет ряд отличительных преимуществ:
- Высокая чувствительность. Метод позволяет обнаруживать даже самые мелкие дефекты, такие как микротрещины и поры, что делает его незаменимым для трубопроводов, работающих под высоким давлением.
- Универсальность. Этот метод можно использовать для различных материалов — от стали до пластиковых труб. К тому же капиллярный метод эффективно работает как на непокрытых, так и на покрытых трубопроводах.
- Отсутствие необходимости в специальном оборудовании. Для проведения контроля достаточно базового набора инструментов и материалов, что значительно снижает затраты.
- Быстрота получения результатов. Инспекция занимает относительно короткое время, а результаты можно получить сразу после завершения контроля.
Несмотря на свои преимущества, капиллярный метод не лишен и некоторых ограничений:
- Чувствительность к загрязнениям: Поверхности, содержащие большое количество загрязняющих веществ, могут препятствовать проникновению жидкости, что приводит к ложным результатам.
- Нельзя использовать на всех типах поверхностей: Некоторые покрытия могут противодействовать адсорбции капиллярной жидкости, что ограничивает применение метода.
- Скорость применения: Хотя капиллярный метод быстр, бывают ситуации, когда для его проведения требуется больше времени, чем для других методов контроля.
Капиллярный метод контроля трубопроводов занимает важное место в арсенале средств неразрушающего контроля. Особенно он полезен в тех случаях, когда других методов недостаточно для выявления скрытых дефектов. При правильном применении капиллярный метод способен значительно повысить безопасность и надежность эксплуатации трубопроводов, что в конечном итоге обеспечивает стабильность работы всего предприятия.
Эффективность и надежность капиллярного метода зависят от квалификации специалистов, которые проводят контроль, поэтому обучение и опыт играют ключевую роль в успешной реализации этой технологии. Направляя усилия на повышение качества визуализации и анализа, предприятия могут предотвратить серьезные аварии и продлить срок службы своих трубопроводных систем.
Магнитопорошковый контроль трубопроводов
Магнитопорошковый контроль сочетает в себе простоту применения и высокую чувствительность к нарушениям целостности материала, что делает его незаменимым в современном производственном процессе.
Магнитопорошковый контроль основан на принципе магнитной индукции и использовании магнитных частиц для выявления поверхностных и подповерхностных дефектов. Этот метод особенно эффективен для ферромагнитных материалов, таких как сталь, которые активно реагируют на магнитное поле.
Принцип работы:
- Магнетизация объекта. Для начала трубопровод подвергается магнетизации. Это может быть достигнуто двумя способами: постоянным магнитом или электромагнитом. В процессе магнетизации создается магнитное поле, которое проникает в материал трубы.
- Нанесение магнитных частиц. После магнетизации на поверхность трубопровода равномерно распределяются магнитные порошки, обычно содержащие железо. Эти частицы могут быть сухими или суспензиями в жидкостях с высокой вязкостью.
- Обнаружение дефектов. Если в трубопроводе имеются трещины, поры или другие дефекты, магнитное поле будет нарушено. Это приведет к тому, что магнитные частицы соберутся вокруг места дефекта, создавая визуально заметный индикатор. Таким образом, специалисты могут легко локализовать и оценить серьезность недостатков.
Магнитопорошковый контроль обладает рядом значительных преимуществ:
- Высокая чувствительность. Метод позволяет выявлять даже минимальные дефекты, что критично для трубопроводов, работающих под высоким давлением.
- Минимальные временные затраты. Процедура контроля может быть выполнена быстро, что сокращает время простоя оборудования и увеличивает общую эффективность производственного процесса.
- Независимость от условий эксплуатации. Метод может применяться в различных условиях, включая высокую влажность и пыль. Это делает его удобным для использования на открытых площадках и в производственных цехах.
Экологические преимущества. Использование магнитных частиц не требует применения химически активных веществ, что снижает экологическую нагрузку и риски для здоровья работников.
Несмотря на множество преимуществ, магнитопорошковый контроль имеет свои ограничения. Метод применяется только к ферромагнитным материалам, что исключает нержавеющую сталь и некоторые полимерные материалы. Кроме того, для обеспечения достоверности результатов требуется высокая квалификация проведения испытаний.
Магнитопорошковый контроль трубопроводов — это высокоэффективный и надежный метод неразрушающего контроля, который помогает обеспечить безопасность и долговечность трубных систем. С его помощью можно значительно снизить риски, связанные с эксплуатацией трубопроводов, сделав их безопаснее для людей и окружающей среды. В условиях современного производства данный метод не только сохраняет время и ресурсы, но и гарантирует высокое качество продукции, что является основополагающим в любой индустрии.
Радиографический контроль трубопроводов
В условиях жестких требований к качеству и безопасности промышленных объектов радиографический метод контроля занимает особое место среди технологий неразрушающего контроля. Этот метод позволяет выявить даже самые мелкие дефекты в структуре трубопроводов, обеспечивая их надежную эксплуатацию.
Радиографический контроль основан на применении рентгеновских или гамма-лучей для визуализации внутренней структуры материалов. Лучи, проходя через материал, поглощаются в зависимости от плотности и толщины. Специальные пленки или цифровые детекторы фиксируют интенсивность прошедшего излучения, создавая изображение, на котором видны дефекты, такие как трещины, пустоты или включения.
Преимущества метода:
- Высокая точность. Радиографический контроль способен выявлять дефекты размером в доли миллиметра, что позволяет своевременно принимать меры по их устранению.
- Глубокое проникновение. Метод эффективен для толстостенных труб и позволяет выявлять не только поверхностные, но и внутренних дефекты, что особенно важно для оценки состояния трубопроводов.
- Наглядность результатов. Полученные снимки обеспечивают визуализацию состояния материала, что упрощает анализ и принятие решений.
Радиографический метод используется в различных отраслях, где критически важна надежность оборудования. Это включает в себя нефтегазовую промышленность, где дефекты в трубопроводах могут привести к экологическим катастрофам, а также в химической и энергетической сферах.
Несмотря на свои преимущества, метод имеет ограничения. К ним относятся необходимость соблюдения мер радиационной безопасности и сложность применения на объектах с нестандартной формой или изломами труб. Кроме того, требуется наличие подготовленных специалистов для интерпретации результатов.
Радиографический метод контроля является надежным и эффективным инструментом в арсенале специалиста по неразрушающему контролю. Он обеспечивает высокий уровень точности при выявлении дефектов и способствует повышению безопасности и надежности трубопроводных систем. Внедрение этого метода на вашем предприятии позволит вам не только соответствовать стандартам качества, но и защитить окружающую среду и предотвратить аварийные ситуации. Такое внимание к деталям поможет вашему бизнесу сохранить репутацию надежного партнера и снизить риски эксплуатации технологических систем.
Ультразвуковой метод контроля трубопроводов
Контроль качества трубопроводов – задача первостепенной важности для промышленных предприятий. Надежность и безопасность эксплуатации зависят от своевременного выявления скрытых дефектов. Одним из эффективных методов контроля является ультразвуковой метод, который предлагает точный и безопасный подход к диагностике состояния трубопроводов.
Ультразвуковой метод контроля (УЗК) основан на применении звуковых волн высокой частоты (обычно от 0,1 до 15 МГц). Эти волны посылаются в материал и, встречая различные неоднородности (трещины, поры, включения и т.п.), частично отражаются, что позволяет вычислить характеристики дефекта. Датчики фиксируют отраженные сигналы, которые затем анализируются с помощью специальных программ.
Преимущества ультразвукового контроля:
- Высокая точность. Ультразвук способен обнаруживать мельчайшие дефекты размером менее миллиметра. Это дает возможность вовремя выявлять даже критические повреждения и принимать меры по предотвращению аварийных ситуаций.
- Безопасность. Ультразвуковой метод не использует ионизирующее излучение, что делает его безопасным для обслуживающего персонала и экологически чистым. Процессы контроля могут проводиться без остановки работы оборудования, что экономит время и ресурсы.
- Универсальность. Метод применим к разным материалам и типам трубопроводов, будь то металл, пластик или композитные материалы. УЗК эффективно работает с объектами сложной формы, в том числе с загнутыми трубами и сварными соединениями
- Технологические особенности. Современные ультразвуковые приборы оснащены различными технологиями для повышения точности и эффективности диагностики. Например, фазированные решетки обеспечивают лучшее разрешение и глубину проникновения благодаря управляемому направлению распространения волн.
Ультразвуковой контроль играет ключевую роль на этапах строительства и эксплуатации трубопроводов. При строительстве он используется для проверки качества сварных швов и выявления дефектов в материалах. В процессе эксплуатации УЗК позволяет оценивать состояние труб, что очень важно для систем с высокими нагрузками или работающих в агрессивной среде.
Ультразвуковой метод контроля трубопроводов является незаменимым инструментом в арсенале современного промышленного предприятия. Его применение позволяет не только гарантировать качество и безопасность эксплуатации, но и сократить издержки, связанные с ремонтом и авариями. Внедряя ультразвук на этапе контроля, предприятия получают уверенность в надежности своих инженерных систем и вклад в долгосрочную устойчивость бизнеса.
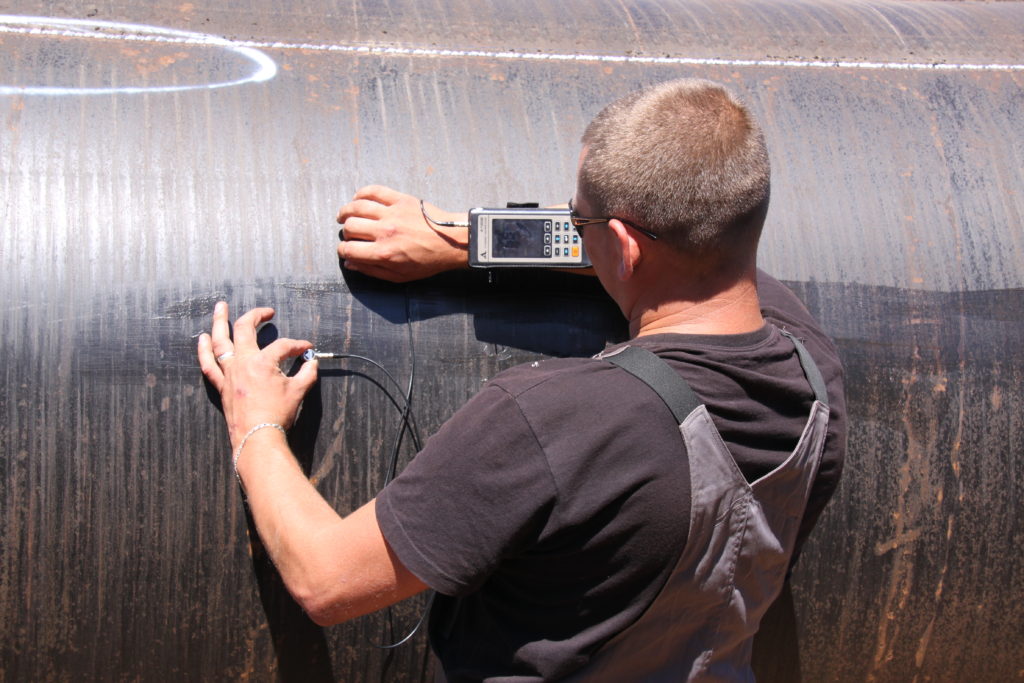
Почему выбирают “ТПЭ-АТОМ”?
Внедрение неразрушающего контроля трубопроводов позволяет значительно сократить расходы на эксплуатацию трубопроводов. Своевременное обнаружение дефектов сокращает простои, снижает объемы аварийных ремонтов и минимизирует ущерб от возможных утечек. Такая профилактическая стратегия снижает страховые премии и повышает доверие инвесторов и партнёров.
Неразрушающие методы контроля представляют собой важный инструмент для обеспечения безопасности и надежности трубопроводных систем. Инновации в этой области продолжают расширять возможности диагностики, предлагая более быстрые, точные и экономически эффективные решения. Внедрение комплексного подхода к неразрушающему контролю позволяет не только сохранить целостность инфраструктуры, но и повысить эффективность работы предприятия в целом. В условиях растущей конкуренции и ужесточающихся стандартов безопасности, инвестиции в НМК становятся жизненно необходимыми для успеха и устойчивого развития бизнеса.
Свяжитесь с нами сегодня, чтобы получить консультацию и профессиональную поддержку по неразрушающему контролю!